Synthese von Bisphenol A (BPA):
- Reaktanzen: Phenol (C6H6O) und Aceton (C3H6O).
- Der erste Schritt ist die Kondensation von Phenol mit Aceton in Gegenwart von Schwefelsäure als Katalysator:
2 C6H6O + C3H6O → C15H16O2 + H2O - Das Ergebnis dieser Reaktion ist Bisphenol A (C15H16O2) und Wasser.
Kondensation von Bisphenol A mit Phosgen:
- Reaktanzen: Bisphenol A (C15H16O2) und Phosgen (COCl2).
- Bisphenol A und Phosgen gehen eine Kondensationsreaktion ein:
C15H16O2 + COCl2 → (C15H16O2)Cl2 + CO2 - Dieser Schritt führt zur Herstellung eines monomeren Copolymers aus Bisphenol A und Phosgen, bei dem Chloratome an einen Bisphenol-A-Ring gebunden sind.
Polymerisation:
- Reaktanz: Monomeres Copolymer aus Bisphenol A und Phosgen [(C15H16O2)Cl2].
- Das Copolymer wird in Gegenwart von Katalysatoren wie Natriumchlorid (NaCl) und Natriumhydroxid (NaOH) polymerisiert:
n[(C15H16O2)Cl2] → (C15H16O2)n + 2nHCl - Dieser Schritt führt zur Bildung von Polycarbonat, das als (C15H16O2)n bezeichnet wird, bei gleichzeitiger Abtrennung von Chlorwasserstoff (HCl) als Nebenprodukt.
Der Polycarbonat-Herstellungsprozess zur Herstellung fortschrittlicher Polycarbonatplatten umfasst die Synthese von Bisphenol A (BPA) und die Kondensation von Bisphenol A mit Phosgen, gefolgt von der Polymerisation von Monomeren zur Herstellung von Polycarbonat. Alle Schritte in diesem Prozess erfordern eine genaue Überwachung der Reaktionsbedingungen wie Temperatur, Druck und Reaktantenkonzentration, um eine optimale Ausbeute und Produktqualität zu gewährleisten.
In der industriellen Praxis ist der Prozess der Herstellung von Polycarbonat komplexer. Neben den grundlegenden Schritten gibt es viele Faktoren, die den Prozess und die Qualität des Endprodukts beeinflussen können.
Wichtige Faktoren, die zu berücksichtigen sind, sind:
- Auswahl der Rohstoffe: Die Qualität und Reinheit von Phenol, Aceton und Phosgen sind entscheidend für die Gewinnung von hochwertigem Polycarbonat. Daher müssen Rohstoffe mit den richtigen Spezifikationen verwendet und sorgfältig analysiert werden, bevor der Prozess beginnt.
- Temperaturregelung: Die Reaktionstemperatur hat einen direkten Einfluss auf die Reaktionsgeschwindigkeit und die Produktqualität. Die Temperatur in den verschiedenen Phasen des Prozesses muss genau überwacht und gesteuert werden, um optimale Bedingungen zu gewährleisten.
- Sicherheit: Phosgen, das bei der Kondensation von Bisphenol A verwendet wird, ist eine gefährliche und giftige Substanz. Es ist notwendig, strenge Sicherheitsmaßnahmen einzuhalten und den Prozess unter kontrollierten Bedingungen durchzuführen, um das Risiko für Mitarbeiter und Umwelt zu minimieren.
- Kondensationsreaktion: Die Kondensationsreaktion von Bisphenol A mit Phosgen ist ein Gleichgewicht und erfordert ein angemessenes Gleichgewicht der Reaktanten und die effektive Entfernung des entstehenden Chlorwasserstoffs. Ein geeigneter Phosgenspender und optimale Mischbedingungen sind essentiell für eine effektive Kondensationsreaktion.
- Polymerisation: Der Polymerisationsprozess von Bisphenol A und Phosgenmonomeren erfordert das Vorhandensein von Katalysatoren wie Natriumchlorid und Natriumhydroxid.
Optimale Katalysatorverhältnisse und die Kontrolle von Polymerisationszeit und -temperatur sind entscheidend, um Polycarbonat mit den richtigen physikalischen und chemischen Eigenschaften zu erhalten.
Zusammenfassend lässt sich sagen, dass der Herstellungsprozess von Polycarbonatplatten ein komplexer chemischer Prozess ist, der High-Tech-Kenntnisse und -Fähigkeiten erfordert.
Eine präzise Überwachung und Kontrolle der Reaktionsparameter sowie geeignete Sicherheitsmaßnahmen sind unerlässlich, um eine hohe Qualität und Leistung von Polycarbonat zu erreichen. Das Verständnis dieser Phasen ermöglicht es Chemieingenieuren, den Prozess zu verbessern und fortschrittliche Technologien für die Herstellung von Polycarbonat zu entwickeln.
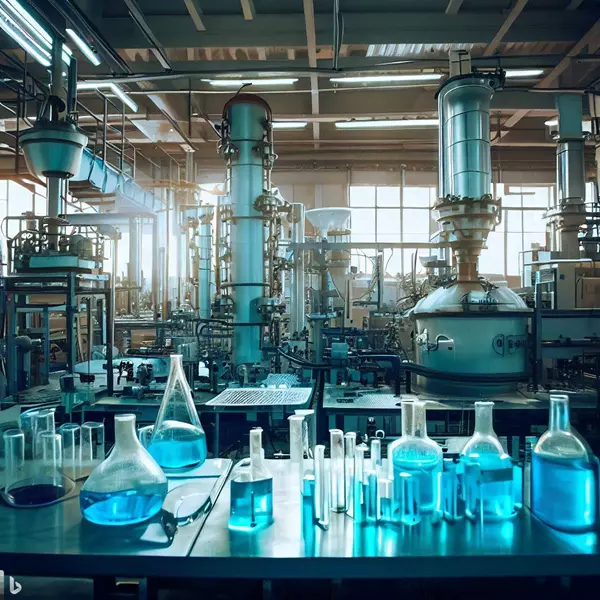
Zukünftige Entwicklungsrichtungen im Produktionsprozess von Polycarbonat
- Katalysatoroptimierung: Die Erforschung neuer Katalysatoren zielt darauf ab, die Effizienz und Selektivität des Polymerisationsprozesses zu erhöhen, was zu Polycarbonat mit noch besseren physikalischen und chemischen Eigenschaften führt.
- Anwendung von Membranreaktoren: Die Verwendung von Reaktormembranen kann zu einer besseren Abscheidung und Rückgewinnung von Nebenprodukten wie Chlorwasserstoff führen, was zu einer höheren Prozesseffizienz und weniger Abfall beiträgt.
- Verbesserung der Recyclingtechnologie: Polycarbonat ist ein langlebiges Material, das Herausforderungen in Bezug auf Entsorgung und Recycling mit sich bringt. Die weitere Erforschung von Polycarbonat-Recyclingmethoden ist entscheidend, um die Umweltbelastung und den Einsatz von Sekundärmaterialien in der Produktion zu reduzieren.
- Optimierung der Reaktionsbedingungen: Die Erforschung optimaler Reaktionsbedingungen wie Temperatur, Druck, Reaktantenkonzentration und Reaktionszeit zielt darauf ab, die Prozesseffizienz zu steigern und die Produktionskosten zu senken.
- Verwendung grüner Rohstoffe: Im Rahmen der Nachhaltigkeit kann die Erforschung der Verwendung von grünen Rohstoffen, wie Biophenol anstelle von Phenol, dazu beitragen, die Umweltbelastung zu verringern und umweltfreundlicheres Polycarbonat zu erreichen.
Der Polycarbonat-Herstellungsprozess zur Herstellung von fortschrittlichen Polycarbonatplatten ist ein komplexer chemischer Prozess, der High-Tech-Kenntnisse und -Fähigkeiten erfordert.
Die präzise Überwachung und Kontrolle der Reaktionsparameter, die Optimierung der Rohstoffe und der Einsatz innovativer Technologien sind der Schlüssel zur Erzielung von Polycarbonat von hoher Qualität und Leistung.
Die Forschung zur Prozessentwicklung, einschließlich der Optimierung von Katalysatoren, des Einsatzes von Membranreaktoren, der Verbesserung der Recyclingtechnologie, der Optimierung der Reaktionsbedingungen und der Verwendung umweltfreundlicher Rohstoffe, zielt darauf ab, den Produktionsprozess von Polycarbonat weiter zu verbessern und zur nachhaltigen Produktion fortschrittlicher Polycarbonatplatten beizutragen.
Herstellungsprozess von Polycarbonat-Sandwichplatten
Extrusion (Extrusion):
- Zubereitung der Mischung: Polycarbonat in Form von Granulat oder Pulver wird mit zusätzlichen Inhaltsstoffen wie Stabilisatoren, Farbstoffen oder Additiven kombiniert, um die mechanischen Eigenschaften zu verbessern. Diese Mischung bildet den Rohstoff für die Extrusion.
- Durchführung des Prozesses: Das Rohmaterial wird im Extruder erhitzt und geschmolzen. Es bildet sich eine homogene Polycarbonatmasse.
- Plattenformung: Die Polycarbonatmasse wird durch eine plattenförmige Düse extrudiert, um eine dünne Schicht aus Polycarbonat mit der gewünschten Breite und Dicke zu bilden.
- Kühlen und Aushärten: Die neu geformte Polycarbonatplatte durchläuft Kühlzonen, die ihre Temperatur senken und ihr die Aushärtung ermöglichen. In einigen Fällen kann das Kochfeld auch in speziellen Wasserkühlbädern gekühlt werden.
- Schneiden und Trimmen: Nach dem Aushärten wird die Platte mit Schneidemessern oder anderen Werkzeugen in die gewünschten Längen oder Formen geschnitten, um fertige Polycarbonatplatten herzustellen.
Vakuumformen:
- Vorbereitung der Form: Die Form, die in der Regel aus Metall oder Kunststoff besteht, wird genau in die gewünschte Form der Polycarbonatplatte gebracht.
- Vorbereitung von Polycarbonatplatten: Die Polycarbonatplatte wird auf die richtige Temperatur erhitzt, um sie flexibel und formbar zu machen.
- Formgebungsprozess: Eine erhitzte Polycarbonatplatte wird über die Form gelegt, und dann wird ein Vakuum zwischen der Form und der Platte erzeugt. Dank dieses Vakuums nimmt das Blech die Form der Form an und passt sich ihren Konturen an.
- Abkühlen und Aushärten: Nach dem Anpassen an die Form wird das Blech abgekühlt, um die neue Form zu fixieren und für strukturelle Stabilität zu sorgen.
- Entnahme und Nachbearbeitung: Nach dem Aushärten wird die Platte aus der Form genommen und anschließend einer Nachbearbeitung unterzogen, wie z. B. dem Laserschneiden in gewünschte Größen und Formen mit Schneidwerkzeugen oder Cuttern. Es kann auch weiteren Bearbeitungsprozessen wie Lochbohren, Biegen oder Biegen unterzogen werden, um die gewünschten geometrischen Eigenschaften zu erreichen.
Es ist erwähnenswert, dass es neben der Extrusion und dem Vakuumformen auch andere Verfahren zur Herstellung von Polycarbonatplatten gibt, wie z. B. die Herstellung durch Ultraschallschweißen oder Mehrschichtlaminierung. Die Wahl der Produktionsmethode hängt von den Anforderungen an das Endprodukt, den Produktionskosten, dem Produktionsumfang und den verfügbaren technologischen Ressourcen ab.
Sobald Polycarbonatplatten hergestellt sind, können sie weiterverarbeitet und in einer Vielzahl von Anwendungen eingesetzt werden. Sie können in kleinere Platten geschnitten, geformt, geklebt, bemalt oder bedruckt werden, um bestimmten Projekten gerecht zu werden. Polycarbonatplatten werden in vielen Branchen wie Bauwesen, Automobil, Beleuchtung, Elektronik, Werbung und vielen anderen eingesetzt.
Zusammenfassend lässt sich sagen, dass Polycarbonatplatten hauptsächlich durch zwei Verfahren hergestellt werden können: Extrusion und Vakuumformen. Beide Verfahren haben ihre Vorteile und sind auf unterschiedliche Produktionsbedürfnisse und -anforderungen zugeschnitten. Der Prozess der Herstellung von Polycarbonatplatten umfasst die Vorbereitung des Rohmaterials, die Formgebung, das Abkühlen und Aushärten, gefolgt von der Nachbearbeitung. Die produzierten Platten können weiteren Verarbeitungsprozessen unterzogen werden, um sie an eine spezifische Anwendung anzupassen.
Polycarbonatplatten werden häufig bei der Herstellung von Oberlichtern und Dachluken verwendet, tragen zur Einführung von natürlichem Licht in Gebäude bei und ermöglichen einen einfachen Zugang zum Dach.
Natürliches Licht ist ein äußerst wichtiger Faktor, der die Atmosphäre und Funktionalität von Räumen beeinflusst. Lichtkuppeln aus hochwertigen Polycarbonatplatten sind die perfekte Lösung, um das natürliche Sonnenlicht optimal zu nutzen. Dank ihrer Transparenz lassen Polycarbonatplatten Licht durch, optimieren die Innenbeleuchtung und schaffen eine angenehme Atmosphäre.
Die Vorteile von Oberlichtern sind zahlreich. Zum einen wirkt sich das natürliche Licht, das durch diese Produkte eingebracht wird, positiv auf das Wohlbefinden und die Gesundheit der Bewohner aus und verbessert die Schlafqualität, die Konzentration und das allgemeine Wohlbefinden. Da Sonnenlicht für die Augen angenehmer ist als künstliches Licht, kann die Verwendung von natürlichem Licht die Belastung der Augen verringern und den Komfort beim Arbeiten und Lernen verbessern.
Darüber hinaus tragen Oberlichter im Dach zur Reduzierung des Stromverbrauchs bei, was sich in finanziellen und ökologischen Einsparungen niederschlägt. Indem Sie das natürliche Licht optimal nutzen, können Sie den Bedarf an künstlichem Licht während des Tages reduzieren, was zu einem geringeren Stromverbrauch und geringeren Kohlenstoffemissionen führt.
Dachzugangsfenster, auch aus Polycarbonatplatten, spielen eine Schlüsselrolle für einen sicheren Zugang zum Dach. Sie bieten eine praktische Lösung sowohl für Wohn- als auch für Geschäftsgebäude. Hergestellt aus langlebigen und langlebigen Materialien wie Polycarbonatplatten, bieten sie nicht nur einen einfachen Zugang zum Dach, sondern auch Schutz vor Witterungseinflüssen und äußeren Einflüssen.
Polycarbonat wird aufgrund seiner vorteilhaften Eigenschaften in verschiedenen Elementen der städtischen Abwasserentsorgung verwendet. Hier sind einige Beispiele für Elemente, die aus Polycarbonat hergestellt werden können:
- Kanalschächte: Polycarbonat wird häufig bei der Herstellung von Kanalschächten verwendet. Diese Sümpfe dienen als Zugänge zum Abwassersystem und ermöglichen so Inspektion, Reinigung und Wartung. Polycarbonat als Strukturmaterial bietet Festigkeit, Beständigkeit gegen Witterungseinflüsse und Korrosion, was für Elemente der städtischen Infrastruktur von entscheidender Bedeutung ist.
- Schachtschutzgitter und -abdeckungen: Viele Schächte sind mit Schutzvorrichtungen und Abdeckungen ausgestattet, um den Zugang zum Innenraum zu schützen und versehentliche Unfälle zu vermeiden. Sumpfabdeckungen aus Polycarbonat sind leicht, langlebig und widerstandsfähig gegen mechanische Beanspruchung und ermöglichen bei Bedarf einen einfachen Zugang zum Sumpf.
- Rohre und Kanäle: Polycarbonat kann auch zur Herstellung von Abwasserrohren und -kanälen verwendet werden. Abwasserrohre aus Polycarbonat sind leicht, korrosionsbeständig und einfach zu verlegen. Sie haben auch eine gute Beständigkeit gegen Chemikalien, was bei der Leitung von Abfallstoffen wichtig ist.
- Fettabscheider: Fettabscheider werden häufig in Abwassersystemen eingesetzt, um Fett und andere Erdölsubstanzen aus fließendem Wasser aufzufangen und abzuscheiden. Polycarbonat kann aufgrund seiner Beständigkeit gegen chemische Substanzen und seiner einfachen Hygiene bei der Herstellung von Fettabscheidern verwendet werden.
- Übergänge und Reduzierungen: In Abwassersystemen können verschiedene Arten von Durchgängen und Reduzierungen erforderlich sein, damit Rohre und Kanäle unterschiedlicher Größe nahtlos miteinander verbunden werden können. Polycarbonat kann zur Herstellung solcher Komponenten verwendet werden, da es leicht zu formen und an verschiedene Abmessungen und Konfigurationen anzupassen ist.
Elemente kommunaler Abwassersysteme aus Polycarbonat zeichnen sich durch Langlebigkeit, Witterungsbeständigkeit, einfache Installation und niedrige Wartungskosten aus. Darüber hinaus ist Polycarbonat auch
Wenn Sie auf der Suche nach hochwertigen Komponenten für Dachsysteme aus Polycarbonat sind, empfehle ich Ihnen dringend, sich an unsere Firma Gulajski zu wenden. Als polnischer Hersteller hebt sich Gulajski auf dem Markt dadurch ab, dass es Produkte von höchster Qualität anbietet, die in polnischer Sprache hergestellt werden.
Es ist erwähnenswert, dass die Firma Gulayski im Gegensatz zu vielen anderen Herstellern keine chinesischen Halbzeuge verwendet. So können Sie sicher sein, dass unsere Produkte aus den besten verfügbaren Materialien hergestellt werden und den höchsten Qualitätsstandards entsprechen. Die Verwendung lokaler Materialien bedeutet auch, dass Sie die polnische Wirtschaft und die Entwicklung der heimischen Unternehmen unterstützen.
Um Elemente des Polycarbonat-Dachsystems von unserer Firma Gulajski zu kaufen, kontaktieren Sie uns bitte unter der Telefonnummer: +48 (32) 236 30 05. Unsere qualifizierten Mitarbeiter stehen Ihnen gerne professionell zur Seite, beantworten Ihre Fragen und stellen Ihnen Ihre Möglichkeiten vor.
Wenn Sie sich für Gulajski entscheiden, können Sie sicher sein, dass Sie qualitativ hochwertige Produkte erhalten, die Ihren Erwartungen entsprechen. Sie profitieren nicht nur von den Vorteilen von Polycarbonat, wie z. B. hervorragenden Lichteigenschaften und Langlebigkeit, sondern können auch sicher sein, dass Sie die lokale Produktion und Wirtschaft unterstützen.
Zögern Sie nicht, kontaktieren Sie uns noch heute und bieten Sie sich professionelle polnische Dachlösungen auf Basis von Polycarbonatplatten an.
Autor: Tomasz Matuszek; Dział Marketingu - Firma Gulajski